As aquaculture production grows, new solutions have been arising to reduce the environmental impact of the industry. Aquafeeds largely contribute to the aquaculture environmental footprint and a Norway-based company, Gas2Feed, is developing solutions to reduce it.
The idea
The company aims to capture and convert CO2 from biogenic sources into nutritional proteins for use in aquafeeds through a fermentation process.
“The inspiration for the technology came from an urgent environmental need to replace plant-based proteins, such as soy, with single-cell proteins (SCPs) in aquafeeds. However, not all of the SCPs are equally sustainable, since some still rely on agricultural goods to be used as feedstocks,” explained Vukasin Draganovic, business development director at Gas2Feed.
“Green microalgae is a good example of highly sustainable ones with only light, CO2, and a few nutrients being used as input elements. Unfortunately, strong cell walls make the recovery of the microalgal contents challenging,” Draganovic stated.
Another exotic microbe, the so-called “knallgas” bacteria, exhibits the same feature as microalgae, placing the CO2 in a cycle (Calvin cycle). “The difference is that they do not need light as an energy source, but instead, they oxidize hydrogen. What is remarkable while growing this organism is that biomass is quite rich in protein and no additional purification is needed,” Draganovic explained.
The process
The company aims to produce microbial protein out of gases: hydrogen, carbon dioxide and oxygen. Unique with the overall concept is that these gases are of a natural origin, simply derived from water and air.
“We get hydrogen and oxygen by alkaline electrolysis, splitting water into these two components. The electrolysis process is in general energy demanding, however, we aim to use only renewable energy sources, hydro, solar or wind,” Draganovic said. The company is partnering with HydrogenPro, one of the world’s largest electrolyzer producers.
When it comes to CO2, the plan is to use only one of biogenic origin. “We are currently developing the technology to extract CO2 from fish farming water, specifically from RAS. The protein production plants can be co-located alongside RAS/land-based farms for CO2 sourcing. Alternatively, bioethanol plants, pulp and paper industry can be good sources of CO2,” Draganovic said.
Biomass with up to 80% protein
Gas2Feed is currently working on optimizing the production process on a pilot-scale plant in Stavanger, Norway. “Preliminary results on product quality are highly promising. We are also in a stage of discussion with our partners for feedstock supply,” Draganovic said.
The protein content in the obtained biomass is about 70%, but it can go up to 80% depending on the processing. “Broadly speaking, the amino acid profile is more similar to fishmeal than to soybean meal,” Draganovic said.
Gas2Feed will start soon testing these SCPs on salmon feeds, “the first of this kind in the industry with this type of product”, according to Draganovic. “The goal here is to develop a tailor-made product that fits perfectly the needs of salmon.”
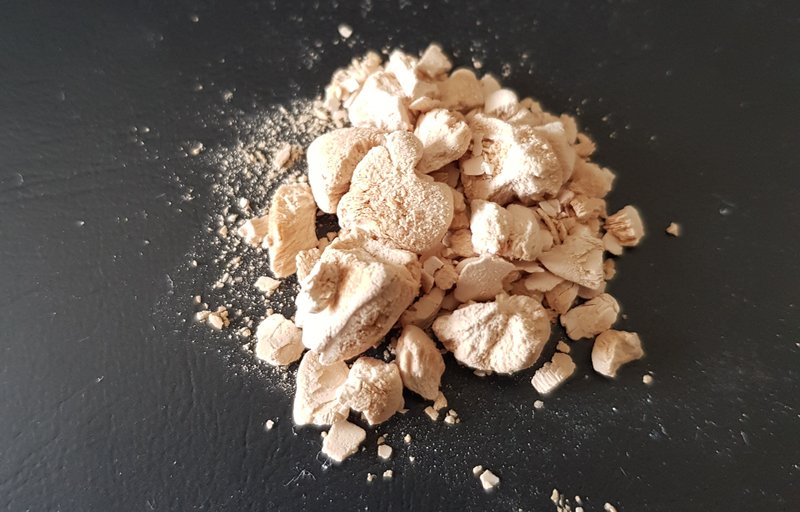
Gas2Feed protein biomass
Environmental benefits
The demand for food is raising at a high pace as the human population grows. Consequently, more forests are cleared and different ecosystems are damaged to accommodate new pastures and cropland. Stockholm Resilience Centre reports that the CO2 in the atmosphere and nitrogen and phosphorus flows have already transgressed the planetary boundaries and are approaching several Earth system thresholds. This can be to a great part ascribed to agricultural processes, the company said.
“We see that more radical approaches are needed and it is urgent to act. Fortunately, technological advancements like Gas2Feed’s process can make a complete disconnection from agriculture. None of the agricultural goods are needed as inputs to microbial protein production. In a so-called ‘agriculture 2.0’ or ‘cellular agriculture’, large volumes of food can be produced in a reactor in a limited area,” Draganovic stated.
According to recent research done by Green Queen Team, transformation towards technologies that convert carbon dioxide into protein can meet global food demands using only 20% of the current farmland. “In other words, we can get 80% of the existing farmland back to nature in about a century. That land can be used to store carbon while also getting back biodiversity,” Draganovic said.
Future prospects
The company recently received a USD 2 million grant from the Norwegian government to support the next development phase. Gas2Feed works closely with NORCE Institute on process and product development and with SINTEF Institute on carbon-capturing technology from fish farms.
2023 is an exciting year for the company. Gas2Feed plans to complete its large-scale pilot/demo facility to produce the protein needed for partners that want to test the product. The Gas2Feed fermentation will be established in connection with its sister company, EcoFishCircle AS, in a land-based salmon farming plant.
Gas2Feed aims to build the first commercial facility in late 2024/early 2025. The plant is expected to produce about 2,000 tonnes of protein per year.